Capacity - How to Find More!
Chris Bujak • April 19, 2021
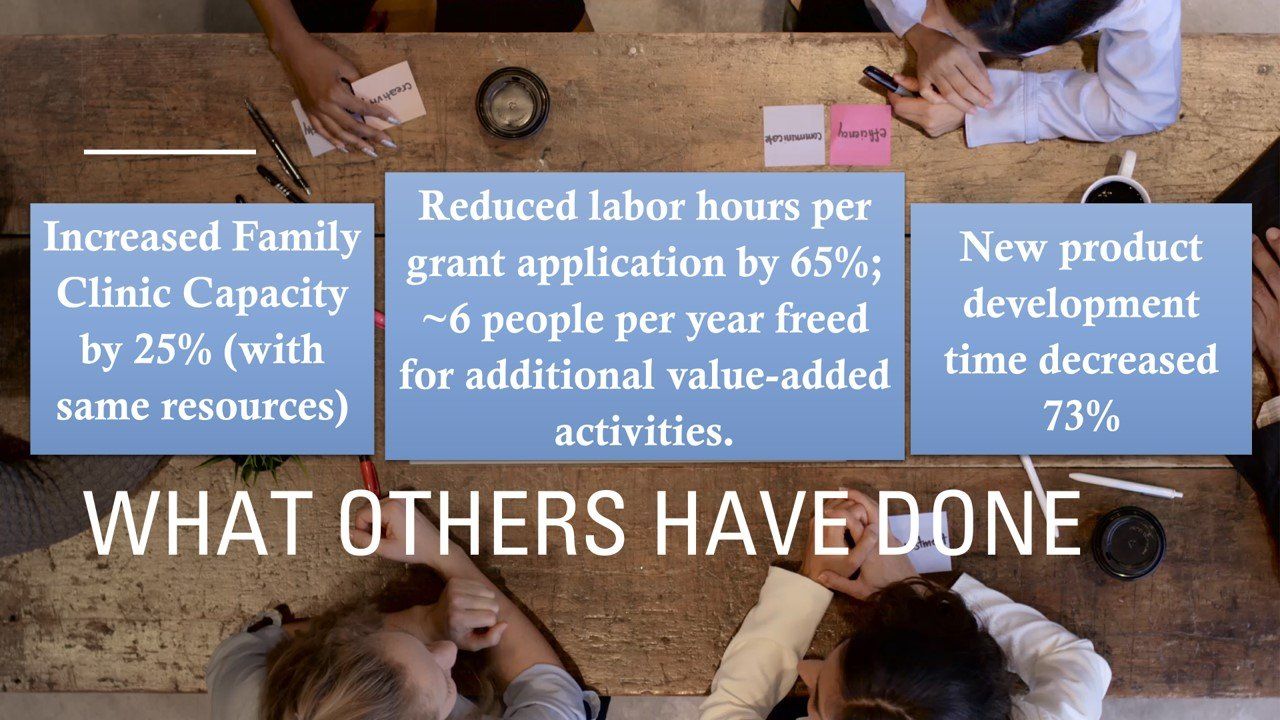
Capacity! We hear capacity references everywhere lately.
Vaccines per day, # Parts created, Struggles to find resources to do the job, Passengers on a plane, Fans in a stadium. What is Capacity? Capacity = the ability to understand and use information to make a decision and perform actions that maximize the amount that someone or something can produce or contain. Free up CAPACITY to accomplish more in the same time, with the same resources, and easier!
Read/Watch to learn more about the innovative ideas and continual quality improvement methods that can help you quickly and effectively expand capacity. Watch to learn more: https://youtu.be/-eKWoRyhg2I
Time and Resources are precious and scarce. Where does more capacity hide?
More capacity can be difficult to find because it is hidden in delays, approvals, defects, and rework loops. Engaging team members performing the work can help identify opportunities to increase capacity:
Wastes that consume resources without adding value and producing output. Work stops! Things Gone Wrong, ugh! Unnecessary movement of people, information, and items! This is no longer needed, yet we keep doing it because we have always done it this way! Getting ready to do the work seems to take up most of the day!
Where are work steps imbalanced (stop and wait for a person or the next step)? Where can resources in the process be freed up or redeployed to keep the work flowing?
When it is a hot job, we can do so much more. Why is not the norm? What is different?
Identifying and working together to eliminate these will increase productivity and capacity. COVID has demonstrated this with the speed of creating and administering vaccines.
Time and Resources are precious and scarce. Here are some ways to maximize your time, resources, and impact.
Use continual quality improvement methods to gain more capacity faster and easier. Relentlessly raise problems and solve them together. Post visual measures and targets to stay focused. Celebrate effort and progress! Applying Kaizen, Flow and Mistake Proofing to processes often produces a cycle time reduction and defect reduction of 50-75%!
1. KAIZEN-Systematic process to rapidly solve problems and implement solutions that stick. More
2. FLOW-Pulling of products, information, or people through a process; one at a time (or minimum batch size), at a formulated and balanced rate; without stopping, waiting, or any delays. More
3. KANBAN-Visual cards, signals, sounds to control the pace of the process, batch size, and material replenishment. No waiting, no runouts. More
4. FMEA-A predictive analysis to identify and anticipate potential failures and their effects, in order to address failures before they happen. More
5. MISTAKE PROOFING-Systematic approach to prevent defects associated with “human error” and avoid the costs, time, and rework resources. More
6. VALUE ENGINEERING-Design / Redesign a product or service so that it only includes value-added steps and parts. More
7. QUICK CHANGE-Changing from one task to another in the most efficient manner. More
8. 5S-5 step method to reduce time spent searching, moving, and getting ready to do work. More
9. STANDARDIZED WORK-Design and document streamlined work process instructions (per role) for consistent and measurable performance. More
10. CAUSE AND EFFECT ANALYSIS-5 step process to identify solutions that fix the root causes of problems so that problems do not return. More
Are these improvement methods worth your time? From our experience in helping expand capacity, we (with no hesitation) say, "Yes"! You can do more, achieve more! Grow team member's value! Reduce stress and feeling overwhelmed! Create happier customers, more customers! Free up CAPACITY – Accomplish more in the same time, with the same resources, and easier!