Flow - Balanced Work - and Kanbans
Chris Bujak • May 3, 2021
Accelerate the speed and improve the quality of a process by eliminating wait times, queue times, and other delays. Significant process improvement can be achieved with the application of flowing one unit at a time (or minimum batch size), with formulated and balanced resource responsibilities and time expectations, and kanbans (visual or automated controls) to manage and signal stop/start of items or information. These methods are best applied to processes with long cycle times, handoffs of work with long wait times, bottlenecks, and poor quality output.
Goal:
To increase knowledge and skills of the Flow, Balanced Work, and Kanban processes and methods and be able to use it to lead a team through realizing signficant time and quality improvements.
Benefits:
- Shorter lead time.
- Happier team members and customers!
- Earlier quality problem discovery
- Less scrap and rework.
- Lower total inventory and higher inventory turns.
Agenda:
Training: 40 hours of education and immediate application. Participants bring a scenario to class on which to focus and practice.
Application and Coaching: On-site event co-lead. One-on-one coaching until results are achieved.
Certification: Participation in this course and completion of 1 project = Continuous Improvement Flow Black Belt CERTIFICATION.
- Understanding the Flow methods.
- Gathering data and information.
- Determining current process variation to balance resource work load.
- Understanding and implementing kanbans.
- Understanding and implementing visual controls.
- Designing the process flow.
- Testing the work process flow and crating sticky implementation of flow, balanced work, kanbans, and visual controls.
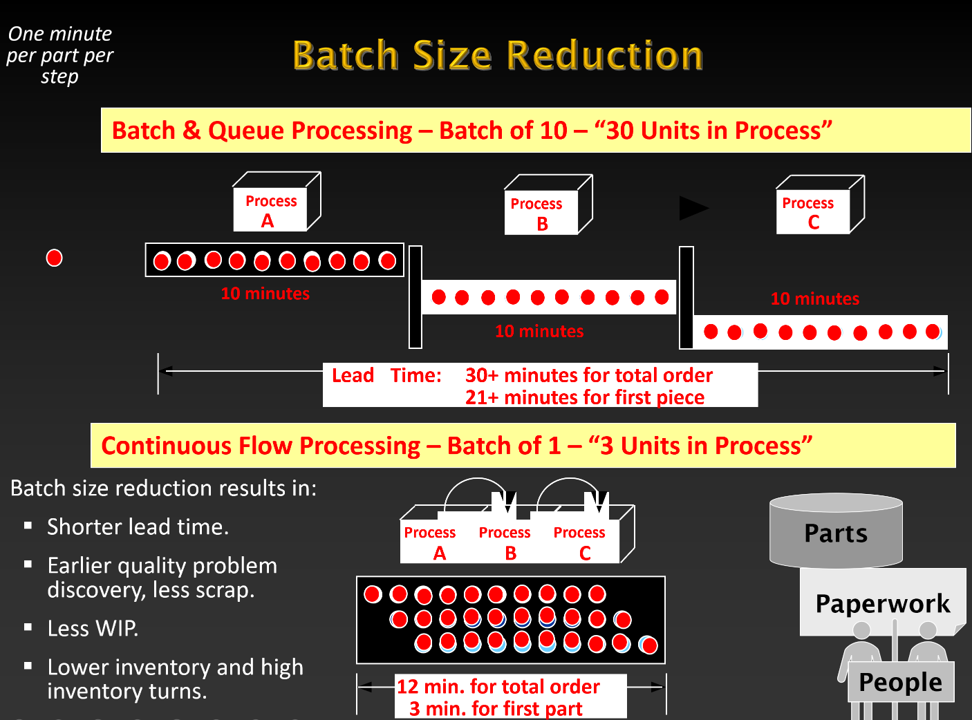