Courses for CI Champions
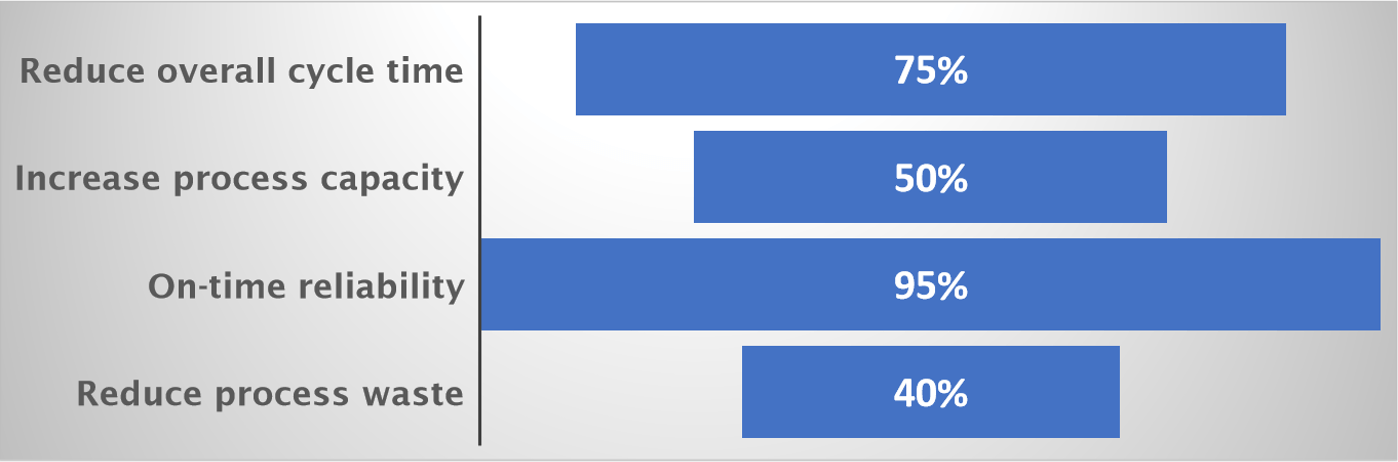
Accelerate the speed and improve the quality a product or process by eliminating wait times, queue times, and other delays. Significant process improvement can be achieved with the application of 1. Flow one unit at a time (or minimum batch size), at a formulated and balanced rate; 2. Kanbans, and 3. visual controls to pull products or information.
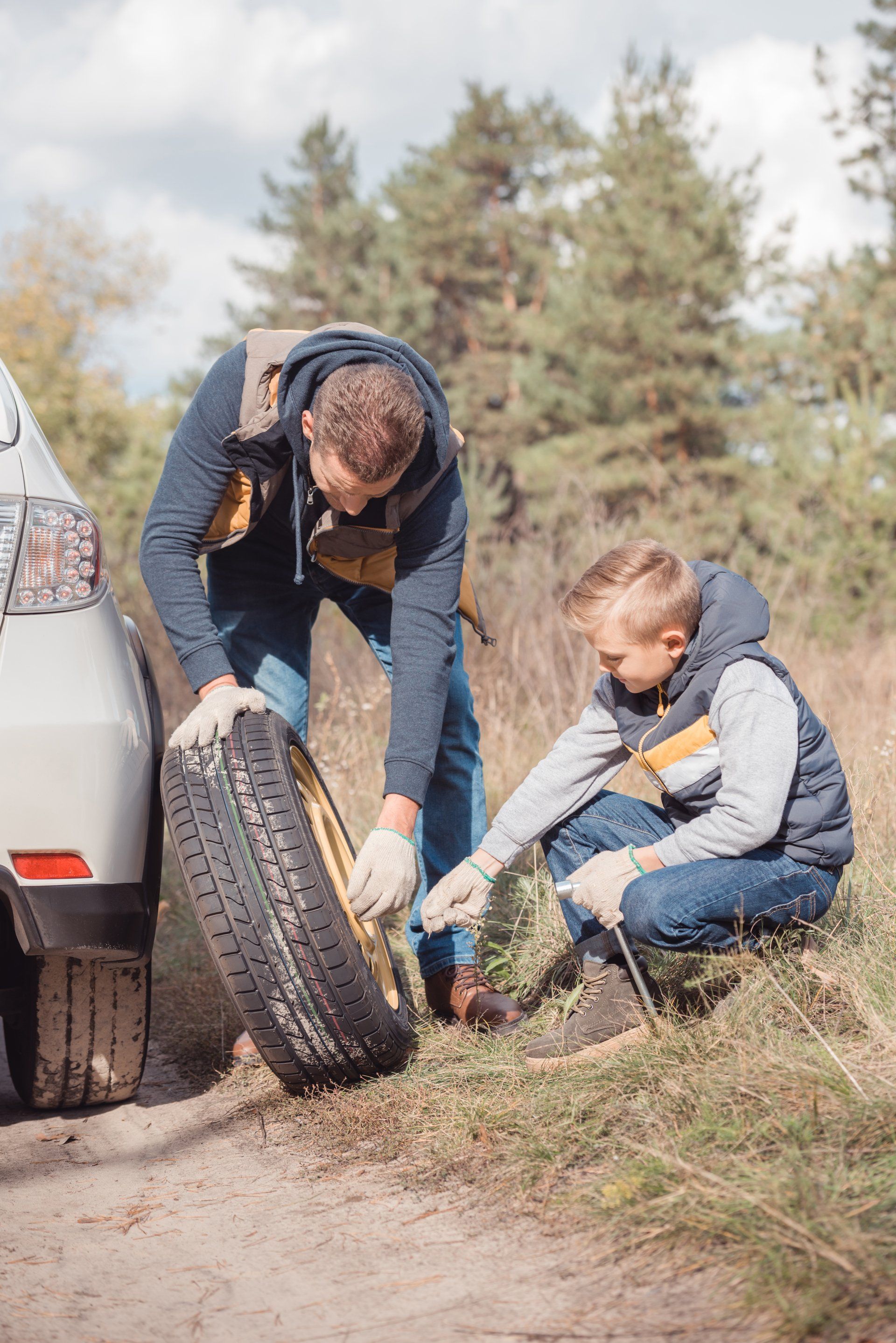
Quick Change / SMED improvements reduce the waste of getting ready to do work. Reductions in changeover times of equipment or processes create immediate and significant benefits in labor productivity, cycle time and inventory. The SMED approach assesses each task of a changeover process to distinguish what can be done externally to the process of changeover and what cannot. The entire work process is then redesigned to eliminate tasks, move external ones out of the changeover process and streamline all remaining activities.
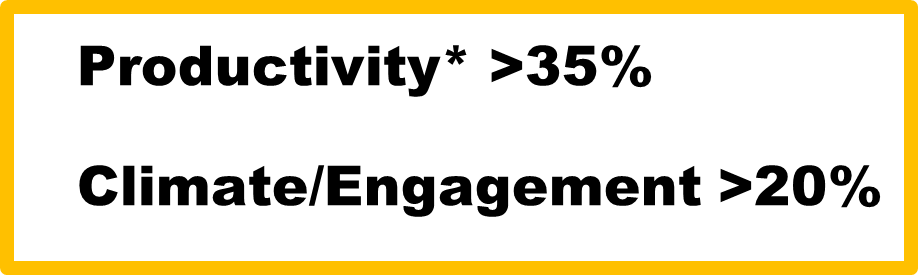
Individuals often report that several hours per day are wasted in searching for materials, equipment, and information needed to do their job! 5S / Workplace Organization Method and Skills teaches you how to help teams get engaged in improvement and create immediate, meaningful, and visual improvement in their workplace.
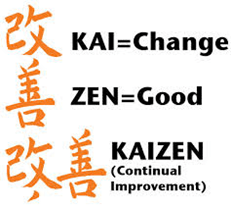
Tired of working 6 months, 9 months, a year to see the benefits of solving a work process problem? This Kaizen education provides the information-based problem solving process to engage and energize teams in creating big process improvements within one week. Yes, all steps of the improvement cycle in 1 week! Stop waiting for change and needed results.
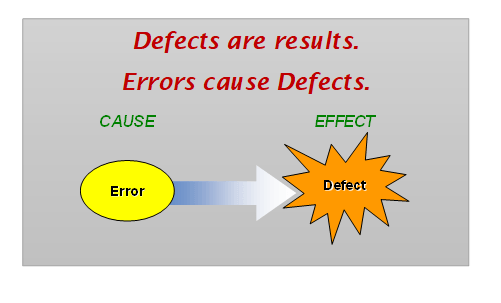
Creating a high-performing work environment where human errors and defects are not accepted. Instead errors and defects are identified, and work processes redesigned to control and minimize the occurrence and effects of human error. Learn help to develop knowledge and skills to effectively and efficiently facilitate the systematic Mistake Proofing approach to prevent defects associated with “human error” and avoid the costs resulting from those defects.
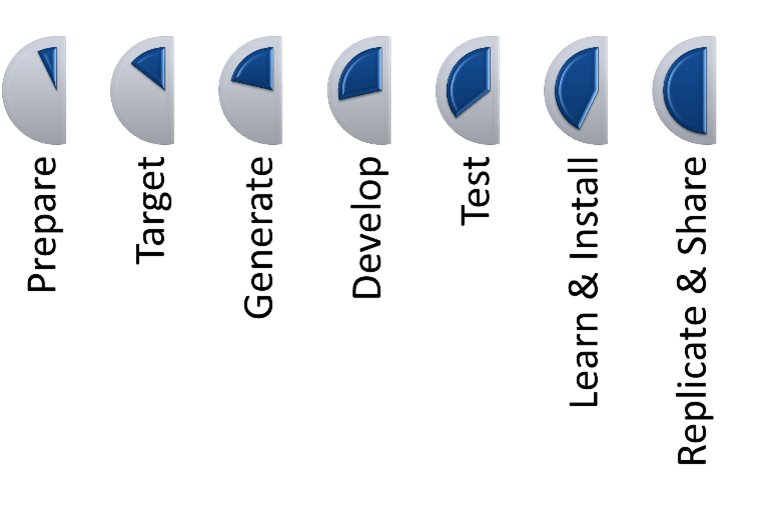
Innovation can be transforming – It can create sizable results for customers and stakeholders and even fun for the team! Unfortunately, a significant number of innovation attempts fail (reported rates of 30% to 80%).
Fortunately, lessons have been learned from the success and failures for others to benefit. This course focuses on the Innovation process and the utilization of improvement methods to create new and innovative products, services, and processes.